Oracle Apps R12 OPM, SCM, INV, Procurement, OM Modules Functional and Technical Solution by Razaul Karim Reza
Translate
Monday, March 27, 2017
PROD_Batch_ Status_Query
SELECT o.ORGANIZATION_CODE, o.ORGANIZATION_NAME, o.ORGANIZATION_ID,
gbh.BATCH_NO,decode(gbh.BATCH_STATUS,3,'Completed') Batch_Status
FROM GME_BATCH_HEADER gbh,
ORG_ORGANIZATION_DEFINITIONS o
WHERE CREATION_DATE between TO_DATE('01-Feb-2017','DD-MM-YYYY') and TO_DATE('28-Feb-2017','DD-MM-YYYY')
AND gbh.ORGANIZATION_ID=o.ORGANIZATION_ID
ORDER BY BATCH_STATUS, o.ORGANIZATION_CODE
Oracle EBs Apps Blog of Mahfuz, OPM Consultant, Bangladesh.
http://mahfuzgeml.blogspot.com/2015/12/opm-formula-to-execution-work-flow.html
Sunday, June 12, 2016
Defining Resource Cost in Oracle Process Manufacturing (OPM) # Defining Fixed Overheads in Oracle Process Manufacturing (OPM) # How to open new period in OPM Cost Calendar? # Subledger Accounting Balances Update # OPM Cost Allocation Process # Setting up default value of Create Accounting mode as “Draft” (Process Manufacturing Financial) #
Defining Resource Cost in Oracle Process Manufacturing (OPM)
To
reflect the cost of the resource incurred during production in the
product cost, set up routings and define the amount or number of
resources used.
Outside
production, set up overheads to reflect the amount of resources other
than the production or ingredients used in the product; you can then
include overhead costs in the cost of producing the product. In either
case, first we must define nominal usage cost associated with the
resource.
To know about defining Overheads, click the following link
Pre-requisites:
Resources
To know about how to define a resource, click the following link
Navigation: OPM Financials > Resource costs
Enter the code of the Organization for which this resource cost is effective.
Note: If
Organization is not entered then the resource cost will be considered
for all the organizations that fall under the displayed Legal entity.
Enter the Resource for which we are defining the cost.
Enter the Cost Calendar & Period for which this resource cost will be applicable.
Component class displays the component class associated with the resource & Base Currency displays the legal entity’s base currency.
Cost Details
Enter for which Cost Type this resource cost is defined.
Enter a Nominal Cost for the resource for using it for one unit of measure. For example,
if you are defining the resource cost for a mixing machine, and its
usage is measured in hours, then enter the cost of using the mixing
machine for one hour.
Enter the unit of measure in which usage of this resource is measured in UOM.
By default the system will display the unit of measure initially
defined for this resource. We can edit the value within the same unit of
measure class.
Note: Status field is not applicable
---X---
Defining Fixed Overheads in Oracle Process Manufacturing (OPM)
An overhead is a cost associated with a resource other than the resource usage assigned in the routing.
Assume
you need a laborer to clean MIXER after each use. To account for the
cost of cleanup, instead of adding another component cost to each item
that uses MIXER, you can assign an overhead to the items being produced
by that laborer on MIXER. The overhead assignment would be the time it
takes the laborer to clean MIXER multiplied by the cost per hour for the
laborer.
Navigation:
OPM Financials > Fixed Overheads
To define Fixed Overheads:
Enter the Item code to which this overhead is going to assigned.
Enter a valid Calendar, Period code & Cost type.
Base Currency code field will display the base currency of the legal entity.
Overhead Details:
Enter the Resource code and Component Class code.
To know how to create a Resource click the following link http://dj-oracleapps.blogspot.in/2014/02/creating-resources-in-oracle-process.html
To know how to create a Resource click the following link http://dj-oracleapps.blogspot.in/2014/02/creating-resources-in-oracle-process.html
Enter the Analysis code under which this overhead should appear in cost detail.
Enter the Qty of resource used in the production of this item in Resource Count. Ex: If it takes one worker to cleanup Mixer after each use, then enter 1. This number is multiplied by the Resource Usage to calculate the total resource usage.
Enter the amount of the resource used for this overhead in Resource Usage. Ex: If it takes 10 minutes for a worker to cleanup Mixer after each use, then enter 0.10
Enter the unit of measure in which the resource is yielded in Resource UOM.
Enter the amount of the item yielded in this production process during the entered .10 hours of resource usage in Item Quantity.
Enter the unit of measure in which this overhead is measured in Overhead UOM field.
---X---
How to open new period in OPM Cost Calendar?
Navigation: OPM Financials > Setup > Cost Calendars
Query the calendar which you use
In the new line enter the Period code, Description & End Date of the period & click ‘Assignments’.
Click on the cost type you are using and click ‘Period Status’ tab.
By default the status of the new period will be ‘Never Opened’.
Click the ‘lov’ and change the status to “Open”.
---X---
Subledger Accounting Balances Update
In this post we will see what Subledger accounting balances update concurrent is & what it does?
The
Subledger Accounting Balances Update is a standalone concurrent program
which calculates the control balances and analytical balances
(supporting reference balances) for any newly accounted transactions.
Normally,
Create Accounting and online accounting will automatically call the
Subledger Accounting Balances Update program to calculate the
control/analytical balances. However, there have been situations where
multiple online accounting programs are called simultaneously, and if
all of them have accounts which belong to either control accounts or
analytical accounts then only one of the simultaneous online accounting
programs will be successful in updating the balances.
To
ensure that balances are up to date, it is recommended that you
manually run the Subledger Accounting Balances Update program for the
ledger at least once before you run the Third Party Balances report or
before viewing Supporting Reference Balances. This is to ensure that all
balances are updated completely.
---X---
OPM Cost Allocation Process
In this post we will see what exactly OPM Cost Allocation Process concurrent does and how to run it.
OPM
Cost Allocation process concurrent takes care of spreading the costs
down to the products as defined in Allocation definitions form.
Parameters:
Legal Entity – Enter your LE
Cost Calendar – Enter the name of your calendar
Period – Enter the period for which the cost has to be allocated.
Cost Type – Enter the costing method which you use.
Fiscal year – Fiscal year
Period – This refers to GL Period
Allocation From - Enter the from allocation code
Allocation To - Enter the to allocation code
Refresh Interface – Yes / No
In the new form enter your Ledger Name and click go.
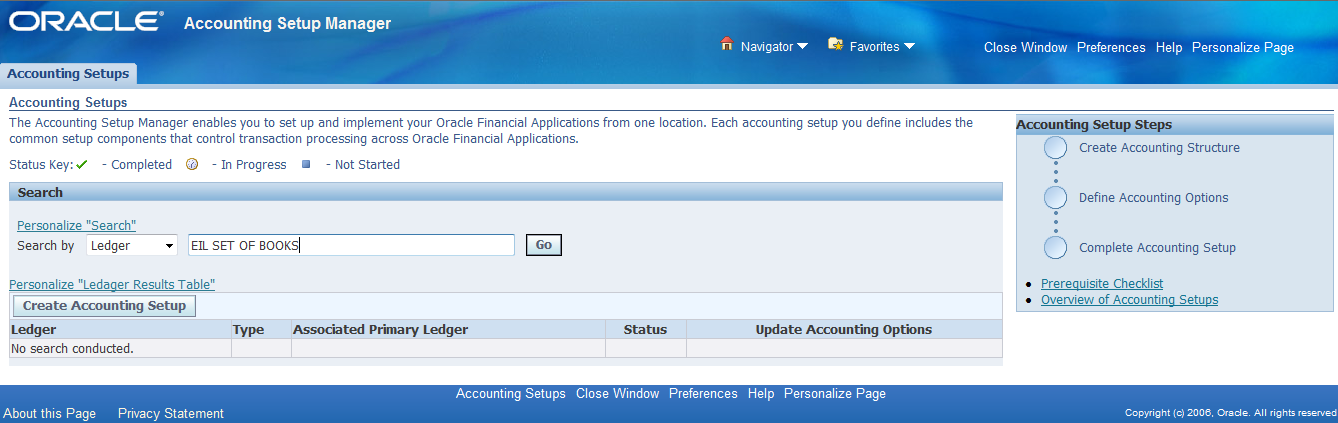
---X---
Setting up default value of Create Accounting mode as “Draft” (Process Manufacturing Financial)
Navigation:
OPM
Financial Responsibility – Setup – Subledger Accounting setups –
Accounting Methods Builder – Methods and definitions – Subledger
Accounting methods.
Query on user defined Subledger accounting method
Keep the cursor on application “Process Manufacturing Financials” & Click “Accounting Setups”.
In the new form enter your Ledger Name and click go.
Click “Update Accounting options” against your Ledger.
Click on “Update” button against “Subledger accounting options” Setup step
In the list of options click “Update Accounting options” against “Process Manufacturing Financials” Application
In the “Accounting Progam Mode” select “Draft”. Click on Apply button.
By following the above steps, we can define the default value of create accounting program as “Draft”.
---X---
Oracle Process Manufacturing(OPM), Actual Cost Adjustments in Oracle R12, Defining Adjustment Reason Codes in Oracle R12, Defining Cost Analysis Codes in Oracle R12, Defining Resource Cost in Oracle Process Manufacturing (OPM), Defining Fixed Overheads in Oracle Process Manufacturing (OPM)
Actual Cost Adjustments in Oracle R12
Actual
Cost adjustment allows us to adjust the final calculated cost of a raw
material or product based on quantity and unit cost.
Navigation:
OPM Financials > Actual costs > Adjustments
Enter the Item for which the cost should be adjusted. This may be a raw material, co-products, by-product, intermediate, or product.
Enter the Cost Calendar to which the adjusted actual costs for the item will be updated.
Enter a Period within the cost calendar to which the adjusted actual costs for the item will be updated.
Cost Type must be an actual cost type.
Item cost field will display the current cost of the Item.
Actual Cost Adjustment Details:
The Actual Cost Adjustment supports three adjustment types,
- Average Cost adjustment
- Value Cost adjustment
- Unit cost adjustment
Average Cost Adjustment:
The
Average Cost Adjustment type lets us to enter a quantity and a cost.
This adjustment simulates a transaction that happened outside the OPM
Actual Cost process. For example, if you use a third party system to
record transactions, then use this adjustment type to replicate the
event to include in cost calculations. The Actual Cost process considers
these transactions similar to a purchase order receipt.
(Prior Qty * Prior cost) + Sum of (Receipt qty * PO price) + Average cost adjustments
New unit cost = --------------------------------------------------------------------------------------------------------
(Prior Qty + Sum of Receipt Qty + Sum of average Cost adjustment Qty)
Value Cost Adjustment:
The
Value Cost adjustment allows us to enter an adjustment value without
quantity. The value entered will be considered for the entire quantity.
(Prior Qty * Prior cost) + Sum of
(Receipt qty * PO price) + Value adjustments
New unit cost = -------------------------------------------------------------------------------------------------
(Prior Qty + Sum of Receipt Qty)
Unit Cost Adjustment:
Unit
Cost Adjustment type lets us to adjust the actual unit cost of the item
with the specified cost. The Actual Cost process calculates the cost of
the item as per the current logic and then applies this unit cost
adjustment to calculate the new adjusted cost. This adjusted cost
becomes the new actual cost of the item.
First the New unit cost (without the Unit cost adjustment) is calculated as follows,
(Prior Qty * Prior cost) + Sum of (Receipt qty * PO price) +
New unit cost Value adjustments + Average Cost adjustments
(without Unit Cost = ---------------------------------------------------------------------------------------
Adjustments) (Prior Qty + Sum of Receipt Qty + Sum of Average Cost adjustment Qty
The
Unit Cost Adjustment is included only after the Actual Cost is
calculated based on the existing Adjustment types. Then, the New Unit
Cost (with the Unit Cost Adjustment) is calculated as follows,
New unit cost (with Unit Cost Adjustments) = New unit cost (without unit cost adjustments) + Unit cost Adjustments
After selecting the type enter the Component Class code being adjusted. To know about defining Component Class click the following link
http://dj-oracleapps.blogspot.in/2014/07/defining-cost-analysis-codes-in-oracle.html
Enter Quantity of the item, if the type is Average Cost Adjustment.
Enter the Unit of Measure
in which the specified item's actual costs are being adjusted in UOM.
This can be any unit of measure that can be converted to the item's unit
of measure.
Specify the new Unit Cost for the item in this inventory organization, calendar and period.
Enter the Reason Code
that defines the reason behind the actual cost adjustment you are
making. To know how to define Reason Code’s click the following link,
Click the Subledger Entry to choose whether a subledger entry should be created for the adjustment.
Note:
Based on the Reason Code
selected, the Subledger Entry defaults what was selected for the
adjustment reason code. For example, if the specified adjustment reason
code was selected as a reason code with the Subledger Entry option
enabled on the Actual Cost Adjustment Codes window, then this field is
automatically enabled.
GL Date
Indicates the GL transaction date used by the Accounting process for
creating accounting entries for adjustments. If the Subledger Entry
option is selected, then the GL Date is enabled and defaults to the
start date of the selected calendar and period. If the Subledger Entry
option is not selected, then the GL Date is disabled and the date is set
to Null.
One of the following three statuses of the costing adjustment displays automatically in Adjustment Status,
- Not Applied - This is the initial status applied to the adjustments
- Applied - This indicates that the adjustments have been "picked up" by the Actual Costing process and have been used in the cost calculation.
- Modified - This indicates that the adjustments have been modified after they have been applied to actual costs.
---X---
Defining Adjustment Reason Codes in Oracle R12
If
there is a need to adjust actual costs calculated by OPM, then use the
Actual Costs Adjustments to enter the adjustment costs. We must specify a
valid reason code to justify the reason for the cost change.
Navigation: OPM Financials > Setup > Actual Costs > Adjustment Reasons
Enter a Code that explains the reason for adjusting the actual cost calculation for a raw material or a product.
Enter a brief Description of the reason.
Enable the Subledger Entry check box to indicate whether to book the adjustment to subledger or not.
---X---
Defining Cost Analysis Codes in Oracle R12
An
individual component cost identified by a particular cost component
class can be further broken down using cost analysis codes for more
granular tracking of costs. The cost analysis codes are used to group
component costs from multiple cost component class types to provide an
alternate view of the total cost.
Navigation: OPM Financials > Setup > Analysis Codes
Enter the Code to identify the cost analysis type.
Enter a Description for the analysis code.
---X---
Defining Resource Cost in Oracle Process Manufacturing (OPM)
To
reflect the cost of the resource incurred during production in the
product cost, set up routings and define the amount or number of
resources used.
Outside
production, set up overheads to reflect the amount of resources other
than the production or ingredients used in the product; you can then
include overhead costs in the cost of producing the product. In either
case, first we must define nominal usage cost associated with the
resource.
To know about defining Overheads, click the following link
Pre-requisites:
Resources
To know about how to define a resource, click the following link
Navigation: OPM Financials > Resource costs
Enter the code of the Organization for which this resource cost is effective.
Note: If
Organization is not entered then the resource cost will be considered
for all the organizations that fall under the displayed Legal entity.
Enter the Resource for which we are defining the cost.
Enter the Cost Calendar & Period for which this resource cost will be applicable.
Component class displays the component class associated with the resource & Base Currency displays the legal entity’s base currency.
Cost Details
Enter for which Cost Type this resource cost is defined.
Enter a Nominal Cost for the resource for using it for one unit of measure. For example,
if you are defining the resource cost for a mixing machine, and its
usage is measured in hours, then enter the cost of using the mixing
machine for one hour.
Enter the unit of measure in which usage of this resource is measured in UOM.
By default the system will display the unit of measure initially
defined for this resource. We can edit the value within the same unit of
measure class.
Note: Status field is not applicable
---X---
Defining Fixed Overheads in Oracle Process Manufacturing (OPM)
An overhead is a cost associated with a resource other than the resource usage assigned in the routing.
Assume
you need a laborer to clean MIXER after each use. To account for the
cost of cleanup, instead of adding another component cost to each item
that uses MIXER, you can assign an overhead to the items being produced
by that laborer on MIXER. The overhead assignment would be the time it
takes the laborer to clean MIXER multiplied by the cost per hour for the
laborer.
Navigation:
OPM Financials > Fixed Overheads
To define Fixed Overheads:
Enter the Item code to which this overhead is going to assigned.
Enter a valid Calendar, Period code & Cost type.
Base Currency code field will display the base currency of the legal entity.
Overhead Details:
Enter the Resource code and Component Class code.
To know how to create a Resource click the following link http://dj-oracleapps.blogspot.in/2014/02/creating-resources-in-oracle-process.html
To know how to create a Resource click the following link http://dj-oracleapps.blogspot.in/2014/02/creating-resources-in-oracle-process.html
Enter the Analysis code under which this overhead should appear in cost detail.
Enter the Qty of resource used in the production of this item in Resource Count. Ex: If it takes one worker to cleanup Mixer after each use, then enter 1. This number is multiplied by the Resource Usage to calculate the total resource usage.
Enter the amount of the resource used for this overhead in Resource Usage. Ex: If it takes 10 minutes for a worker to cleanup Mixer after each use, then enter 0.10
Enter the unit of measure in which the resource is yielded in Resource UOM.
Enter the amount of the item yielded in this production process during the entered .10 hours of resource usage in Item Quantity.
Enter the unit of measure in which this overhead is measured in Overhead UOM field.
---X---
Setting up Validity rules for Recipe in Oracle Process Manufacturing (OPM)
By
using Validity Rules an organization can set the standard quantity and
effective dates of a recipe to specify what, where, when, and how
formulas, recipes, routings, and operations must be applied.
Prerequisite:
- Recipe
To know how to create a recipe, click the following link.
Navigation: Process Engineer > Recipes
Query the recipe for which the validity rule is going to be set & Click Validity Rules tab.
Enter the Organization that owns this Validity rule.
Validity Rule
Select Recipe Use as,
- Production for use in production of products.
- Planning for use in planning material consumption.
- Costing for use in establishing costs.
- Regulatory for use with hazardous or controlled materials.
- Technical for use in establishing technical classes and subclasses.
Enter a Product in the formula for the validity rule.
Enter the Preference
number for the validity rule. When more than one formula can be used to
produce the same product, this field indicates the validity rule that
must be used first, second and so forth.
Enter the Standard Quantity
of product made with the formula. This quantity is only used for
product costing. It does not restrict quantities that can be produced
with the formula.
Enter the Minimum Quantity of product that can be made using the Formula.
Enter the Maximum Quantity of product that can be made using the formula.
Theoretical displays the theoretical process loss based on the Validity Rule Standard Quantity.
Enter Planned Process Loss. This overrides planned process loss entered at the routing level.
Enter Fixed Process Loss. This value is defaulted to the value you entered in the Recipe Details window. If required, we can override this value.
Enter From date
as the date the validity rule becomes effective. The date must be
within the effective date for any routing associated to the recipe.
Enter To date
as the date to stop using the validity rule. If an expiration date is
not defined for the validity rule, then this is an optional field and
must be left blank.
Step Quantity
The fields are view only.
Operation associated to the step will be displayed.
Step Quantity and its UOM indicate the quantity processed by the routing step and the unit of measure of the step quantity.
Now
a validity rule is set for this Recipe. The system will not allow us to
create a batch with this recipe, even if any one of the condition in
the validity rule fails.
Note:
A
validity rule cannot be approved for general use until its associated
recipe is approved for general use. We can change the status of recipes
or validity rules to on-hold or obsolete even if they are used in
batches as long as all the batches are closed or canceled.
ORA-06503: PL/SQL Function returned without value in Package INV_Validate_Trolin Procedure Attributes
When trying to create a new batch, following error is occurring:
ORA-06503: PL/SQL Function returned without value in Package INV_Validate_Trolin Procedure Attributes
Cause:
The
issue is occurring when, an item is used in the formula with an UOM
that is neither primary or secondary item UOM and there is no conversion
defined between the formula UOM and primary or secondary UOM.
Solution:
Check
whether wrong UOM is entered mistakenly in Formula. If UOM’s were
entered as required then define correct UOM conversions for items used
in formula.
---X---
===X===
Subscribe to:
Posts (Atom)
Item Rate Update for Stock In Trade - Returnable Receive/Return (Loan)
Stock In Trade - Returnable Receive/Return (Loan)
-
Oracle Apps R12 Subledger Accounting Tables and joins XLA Table joins GL_JE_BATCHES (je_batch_id) => GL_JE_HEADERS...
-
Oracle Forms: How to select multiple records in a block using a Record Group I decided to create this demo because the question of how to s...
-
1. Oracle Receivables -> Setup -> System ->System Options a. Receivable GL related setup b. Transaction and Customer rela...